공정 제어 경화 터닝 셀은 18일 만에 투자 비용을 되돌려줍니다
Equator 프로그래밍 가능 게이지는 베어링 가공 및 부품 분류를 위한 최고의 자동화 셀을 구축하는 데 도움이 됩니다.
미국텍사스 콘로 – Conroe Machine은 '자체 제어' 공정을 운영하는 무인 셀에서 24시간 내내 부품을 경화 터닝하는, 대부분의 기계 작업장의 꿈만 같은 작업을 해내고 있습니다. 이곳에는 트윈 스핀들 Okuma 2SP-250 선반의 100% 부품 검사 및 자동 보정을 위해 Renishaw EZ-IO 소프트웨어를 사용하여 간단한 종합적 통신 기능을 제공하는 Equator 측정 시스템 탑재 FANUC 로봇이 설비되어 있습니다. 이 설비는 또한 완성된 부품을 포장하여 운반까지 합니다. 회사는 놀랍게도 터닝 설비 비용을 18일만에 회수할 수 있었다고 말합니다.
Conroe의 사례는 CNC 프로그래머인 James Wardell과 로봇 기술자인 Jeff Buck이 개발한 소프트웨어 및 프로그래밍과 함께 Renishaw의 프로그램 가능 Equator와 같은 새로운 기술을 활용하는 오늘날 젊은 자동화 전문가의 재능만 있다면 어떤 작업장에서도 이와 같은 일이 가능하다는 사실을 잘 보여줍니다. 이 자동화 팀은 여기서 더 나아가 고객을 위해 Equator 2대, FANUC 로봇 1대, 비전 시스템 및 여러 레인의 로우 프로파일 컨베이어로 구성된 자동 부품 측정/분류 셀도 제작했습니다. 두 사례 모두에서 Equator는 고정 장치를 사용하지 않고 비용 효율적으로, 또는 작업장 환경에서 아무 문제 없이 일련의 베어링 레이스를 신속하게 측정함으로써 프로그램 가능 비교 검사의 가치를 입증합니다.
Conroe Machine은 현존 최고의 제조 기술을 이용한 부품 생산이라는 명확한 목표를 가지고 2000년도 Murray ‘Tippy' Touchette에 의해 창립된 비교적 젊은 기업입니다. 이 회사는 온습도가 조절되는 65,000평방피트(6000평방미터) 규모의 플랜트에서 약 150명의 직원이 일하는 규모로 빠르게 성장했습니다. 일반 작업장이지만 Conroe는 휴스턴에 인접해 있어 석유 및 가스 산업에서 주로 시추 구성품 제작 작업이 많은 비율로 수주되고 있습니다. 이 업계에서 지속적으로 들어오는 작업 중 하나는 다운홀 머드 모터용 스러스트 베어링 레이스 제조입니다. 이러한 부품은 매주 수천 개씩 쉬지 않고 생산됩니다.
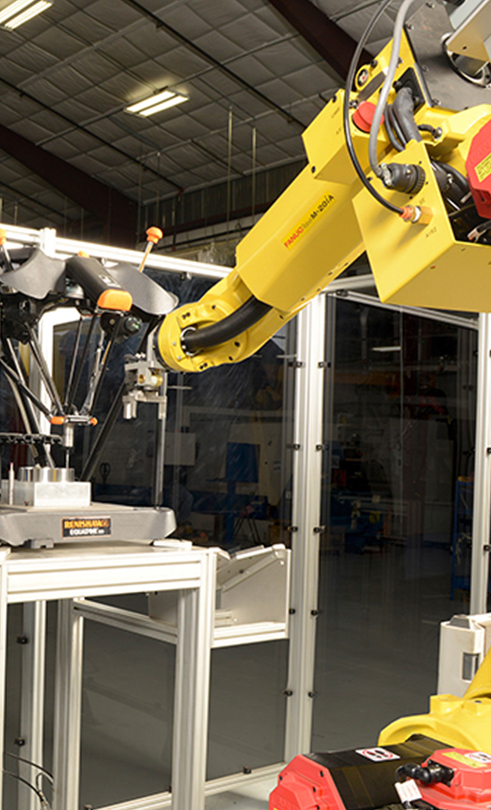
자동화 수준 개선
현재 베어링은 4대의 Doosan Puma 선반에서 대략적 작업을 마치지만 이전에는 4명의 작업자가 동원되어 대략적 작업과 마무리 작업을 수행했습니다. 이러한 기계는 현재 두 개의 셀로 분할되어 FANUC 로봇에 의해 작업물이 올려지고 내려지면서 대략적 작업만 수행합니다. 이러한 셀은 이 작업장의 초기 자동화 프로젝트의 결과물입니다. 절반이 완성된 부품은 마무리 터닝 전에 내보내져 0.070인치(1.7mm) 깊이에서 HRC 65로 케이스 경화됩니다.
James Wardell은 “이 두 개의 셀을 사용하여 생산량이 하루 800-1000개로 안정화되었습니다. 셀당으로 따지면 400-500개입니다. 한 명의 작업자가 기계를 적재하고 부품을 검사합니다. 그러나 이처럼 많은 생산량의 많은 부품을 한 명의 작업자가 올바르게 검사할 수 있으므로 더 많은 생산이 필요했습니다.”라고 설명합니다.
왜 Equator인가?
그는 “다음 셋업을 위해 자동 부품 로딩, 공정 후 측정, 자동 공구 보정, 부품 인그레이빙 및 부품의 박스 포장/팔레트 올리기 등을 포함하여 마무리 가공을 위한 완전 자동화 공정을 구상했습니다. 이러한 시스템의 구성 요소에 대해서는 상당히 잘 알고 있었지만 공구 보정을 위한 부품 측정 기술, CNC 유형 및 소프트웨어에 대해서는 그렇지 못했습니다. 짧게는 98초 밖에 되지 않는 부품의 사이클 시간을 감안하여 검사 속도가 빨라야 합니다. 처음에는 속도가 빠른 백색광 레이저 검사를 생각했지만 부품의 반사가 너무 심합니다. 하드 게이징과 제조 현장 CMM도 살펴보았습니다. 하드 게이징은 너무 고가였고 셋업에 주의가 필요했으며 CMM에는 속도 이점이 없었습니다. 다른 프로젝트에서 Renishaw와 협력했던 경험이 있는 지역 관리자인 Sheila Schermerhorn이 저희에게 Equator를 가능한 솔루션으로 소개해주었습니다.”라고 덧붙입니다.
저희 가공 셀에서 Equator와 비교할 만한 비용 효율적인 작업장 측정 도구는 없습니다.
Conroe Machine (USA)
공정 제어 공구 및 소프트웨어
Equator는 전용 측정에 비해 저렴하고 유연한 대안으로서 비교 측정 방법을 사용합니다. Equator의 '마스터링'을 위해 CMM에서 측정한 알려진 수치를 가진 마스터 부품이 사용되며 이후의 모든 측정은 마스터와 비교됩니다. 마스터링 직후의 반복정도는 0.00007인치(0.002 mm)입니다. 작업장의 온도 변화를 보정하기 위해 Equator는 언제든지 다시 마스터링할 수 있습니다. Equator는 초당 최대 1000포인트의 속도로 접촉 및 스캔 데이터를 수집하기 위해 SP25 프로브를 사용합니다. 스타일러스는 일체화된 6포트 교환 랙에 보관되며 MODUS™ Equator 소프트웨어를 통해 시스템을 프로그래밍합니다. Equator는 누름 버튼을 이용해 수동 방식으로 편리하게 사용할 수 있지만, 이 사례에서는 자동화를 위한 EZ-IO 소프트웨어와 함께 Conroe의 자동화 시스템에 통합하기에 이상적으로 설계되었습니다.
Wardell은 “2012년 초 하트위그에서 참관장에 참여하여 Okuma의 트윈 스핀들 이중 Gantry 선반과 함께 Equator가 사용되는 모습을 보았습니다. 저희가 다루는 유형의 부품에 즉시 자동화가 가능하다는 점 외에도 선반의 Windows® 기반 OSP 이중 경로 컨트롤에는 개방 아키텍처의 PC 기반 운영 플랫폼이 포함되어 있습니다. 자체 자동 보정 소프트웨어를 개발하려는 저희의 계획에서 이러한 부분은 중요했습니다.”라고 말합니다.
자동화 셀의 Equator
Wardell과 Buck은 계속하여 Okuma 2SP-250H, Equator 1대, 인그레이빙 기계 및 FANUC M20iA 6축 로봇으로 구성된 셀을 설치하였습니다. 실제로 두 부분으로 이루어진 선반의 캐루젤에는 부품 약 300개의 원시 공작물이 적재됩니다. 선반의 이중 Gantry 로더가 스핀들을 주입시키고 완성된 부품을 활송 장치에 놓습니다. 이 활송 장치는 로봇이 부품을 픽업하기 위한 컨베이어로 연결되어 있습니다. 로봇은 측정을 위해 부품을 Equator에 놓고, 허용되는 경우 이를 인그레이빙 기계로 전달한 다음, 마지막으로 완성된 부품을 박스 포장하고 팔레트 위에 놓습니다.
Wardell은 “저희는 OSP 컨트롤에서 실행하기 위한 자체 공구 보정 소프트웨어를 개발했습니다. 이 소프트웨어는 CSV 파일 형식으로 전달되는 Equator의 측정 결과를 사용하여 부품이 공차에서 벗어날 때 공구를 오프셋시킵니다."라고 덧붙입니다. 가공으로 부품의 각 측면에서 약 0.015인치(0.38 mm)가 제거되며, 이때 가장 여유가 없는 공차는 ±0.001인치(0.025 mm) 및 8마이크로인치(0.5 micron)의 표면 마무리입니다. 부품의 외경 크기는 약 3인치에서 6인치까지입니다. Wardell은 “Equator는 충분한 여유를 두고 공차 내에서 쉽게 측정을 수행할 수 있습니다."라고 말합니다.
공정 제어
“OD/ID는 정확하게 유지되며 반경에서의 차이는 약 5미크론 정도입니다. 저희는 부품을 크기별로 일괄 처리하므로 척 조와 다른 공구를 교환해야 할 필요성이 최소화됩니다. Equator는 속도가 빨라 공정 속도를 쉽게 따라갈 수 있습니다. 작업장 온도가 72 °F”(22.2 °C)로 제어되므로 하루에 한 번만 마스터링을 다시 수행합니다."
검사 원리 및 자동화된 유연성
부품의 측정 방법은 놀라울 정도로 단순합니다. Wardell은 “가운데 구멍이 있는 알루미늄 블록을 만들어 Equator 고정 플레이트 중앙에 놓았습니다. 이 블록을 사용하여 중앙을 결정하고 좌표계를 설정합니다. 각 부품은 이 블록의 중앙에 놓입니다. 접촉을 통해 부품의 중앙 위치를 얻고 나머지 모든 부분에 대해 표면을 스캔합니다. 부품 고정 장치나 스타일러스 교환 없이 측정 프로세스가 작동하도록 계획했습니다. Equator의 EZ-IO 자동화 소프트웨어를 통해 로봇이 각 부품 유형에 대해 실행할 측정 프로그램을 선택합니다. 저희는 부품을 공차 내에서 유지하기 위해 측정해야 하는 중요 형상을 알고 있습니다.”라고 설명합니다.
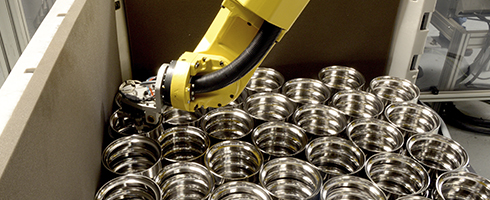
사용된 부품 측정/분류
경화 터닝 셀은 현재 하루 약 600-700개의 완성품을 생산하고 있어 이전의 두 개와 비교하여 지금은 하나의 셀만 필요합니다. 지금은 한 고객을 위해 부품 분류가 가능한 후속 프로젝트가 추진되고 있습니다. Touchette가 도안한 개념을 바탕으로 Wardell과 Buck은 사용된 머드 모터 스러스트 베어링 레이스를 위한 측정 및 분류 셀을 개발하고 있습니다.
유전 서비스 작업장에서 사용된 모터가 분해되고 정비를 거친 후 다시 사용 환경으로 되돌려집니다. Wardell은 “고객은 사용된 레이스를 육안으로 검사하여 부품이 재사용 가능한지 결정하고 있는 실정이어서, 고객 스스로도 쓸만한 부품이 버려지고 비용이 낭비된다는 사실을 알고 있습니다. 쓸만한 레이스가 버려지지 않도록 공정에서 사람의 판단력을 배제시키는 플러그 앤 플레이 측정 및 분류 시스템을 제공하려고 했습니다."라고 말합니다.
이 기사가 작성될 당시까지도 개발에 여념이 없던 Buck과 Wardell은 Equator 2대, FANUC LRMate 200iC 6축 로봇, 여러 레인의 로우 프로파일 컨베이어, FANUC iR 비전 시스템 및 로봇 단말 작동기용 ATI 고속 공구 교환기로 구성된 셀을 조립하고 있습니다. 비전 시스템은 표시된 부품 번호와 실행할 측정 프로그램을 Equator에 알려줍니다. 이후 양호한 부품은 해당 컨베이어에 배치되고 불량 부품은 폐기물 컨베이어에 놓입니다.
Buck은 “저희는 하나로 일체화시켜 이 시스템을 트럭에 실을 수 있도록 설계했고 모터 작업장 관계자들이 사용하기에도 편리하도록 설계했습니다. 전원을 켜고 부품을 컨베이어에 적재하기만 하면 됩니다”라고 말합니다.
Wardell은 “저희 가공 셀에서 Equator와 비교할 만한 비용 효율적인 작업장 측정 도구는 없습니다. “고객을 위한 셀 통합 시도가 이 분야에서 저희 회사에 새로운 비즈니스 기회의 문을 여는 계기가 되기를 희망합니다.”라고 덧붙입니다.